The Precision Power of CNC Aluminum Parts in Modern Manufacturing
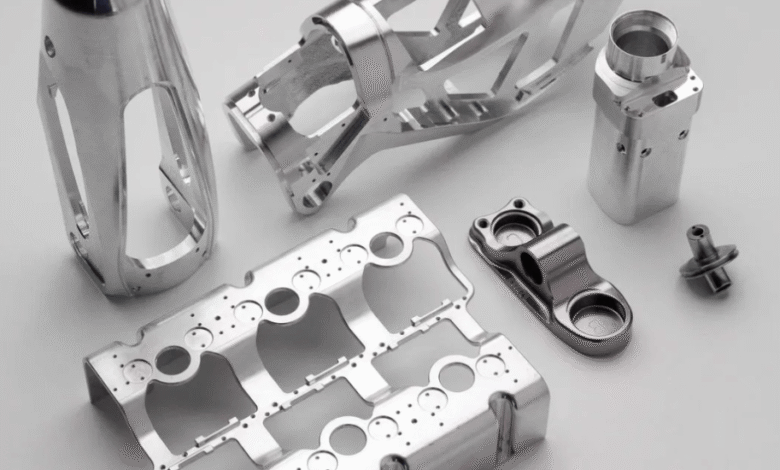
In the age of advanced manufacturing, precision and performance are non-negotiable. From aerospace to medical devices, today’s industries demand components that meet the highest standards of accuracy, durability, and consistency. At the center of this technological revolution are cnc aluminum parts—components created using computer numerical control (CNC) machines and high-quality aluminum alloys. These parts play a vital role in innovation, product development, and high-volume manufacturing.
This article explores why cnc aluminum parts are the go-to choice across industries, how they’re made, their benefits, and their growing role in global manufacturing ecosystems.
What Are CNC Aluminum Parts?
CNC aluminum parts are components manufactured from aluminum stock using CNC (Computer Numerical Control) machines. These machines follow pre-programmed instructions to cut, shape, and finish aluminum with extreme precision. The process ensures consistent results with tight tolerances, regardless of production volume.
These parts can range from tiny brackets and fasteners to complex housings and aerospace-grade mechanical parts. Thanks to CNC technology, manufacturers can achieve mass customization with outstanding repeatability and efficiency.
See also: Exploring the Role of 18662719305 in New Age Tech Solutions
Why Use Aluminum for CNC Machining?
Aluminum is one of the most popular metals in CNC machining—and for good reason. Its material characteristics make it an ideal candidate for applications that demand performance, light weight, and cost-effectiveness.
Key Benefits of Aluminum in CNC:
- Lightweight yet Strong: Aluminum is about one-third the weight of steel but still offers impressive strength.
- Highly Machinable: Compared to harder metals, aluminum is easier to cut, drill, and shape, reducing machine wear and production time.
- Corrosion Resistance: Aluminum naturally forms an oxide layer that protects it from corrosion, ideal for marine, automotive, and medical applications.
- Excellent Thermal and Electrical Conductivity: Perfect for heat sinks, enclosures, and connectors.
- Cost-Effective: Its fast machining time and recyclability make aluminum a budget-friendly option.
Common CNC Aluminum Alloys Used
Different alloys are used depending on the performance required from the cnc aluminum parts:
- 6061-T6: Most commonly used; good corrosion resistance, mechanical strength, and weldability.
- 7075: High strength-to-weight ratio; often used in aerospace and military applications.
- 2024: Excellent fatigue resistance and strength; commonly used in structural components.
- 5052: Superior corrosion resistance and formability; ideal for marine environments.
Each alloy offers different strengths and trade-offs, so material selection depends on the project’s specifications.
The CNC Machining Process for Aluminum Parts
Creating cnc aluminum parts involves multiple steps, all guided by digital precision. Here’s a typical production workflow:
1. CAD Design
Every project begins with a CAD (Computer-Aided Design) file that outlines the geometry, features, and tolerances of the part.
2. CAM Programming
The CAD file is translated into CAM (Computer-Aided Manufacturing) software, which creates toolpaths for the CNC machine.
3. Material Selection and Fixturing
Raw aluminum bars or sheets are secured in the CNC machine. Fixturing ensures the part stays stable during machining.
4. Machining Operations
The CNC machine performs milling, turning, drilling, tapping, or grinding operations based on the toolpaths. Common types of CNC machines used include:
- CNC Mills: Remove material using rotating cutters.
- CNC Lathes: Best for symmetrical parts like shafts or pins.
- Multi-Axis CNC Machines: Handle complex geometries with fewer setups.
5. Finishing
Post-processing includes deburring, sanding, anodizing, or coating to improve surface finish, appearance, or corrosion resistance.
Applications of CNC Aluminum Parts
CNC aluminum parts are essential across a wide range of industries:
🚀 Aerospace
Weight reduction without compromising strength is key. CNC aluminum parts are used in structural brackets, housings, frames, and interiors.
🚘 Automotive
From engine blocks to dashboards and battery enclosures in EVs, aluminum components offer performance with efficiency.
🩺 Medical Devices
CNC aluminum is used to make surgical tools, diagnostic machines, and housings due to its cleanliness, resistance to bacteria, and machinability.
📱 Electronics
Aluminum’s heat dissipation qualities make it perfect for CNC-manufactured enclosures, frames, and radiators in laptops, smartphones, and routers.
⚙️ Industrial Equipment
From robotics arms to automation systems, aluminum parts allow for lightweight yet durable machinery components.
Advantages of CNC Aluminum Parts
The advantages of using cnc aluminum parts go beyond just material benefits. CNC machining elevates the possibilities:
- Precision and Accuracy: Tolerances as tight as ±0.001 mm can be achieved.
- Consistency in High Volume: CNC machining allows the same quality across thousands of units.
- Complex Geometries: Multi-axis machines can create complex features not possible with manual machining.
- Fast Turnaround: Reduced lead times compared to other manufacturing methods.
- Design Flexibility: Rapid prototyping capabilities allow designers to test and tweak parts quickly.
Surface Finishing Options for CNC Aluminum Parts
Aluminum is extremely receptive to surface treatments, which not only improve appearance but enhance durability.
- Anodizing: Provides corrosion resistance and coloring options.
- Powder Coating: Adds a protective, decorative layer.
- Bead Blasting: Offers a uniform matte finish.
- Brushing/Polishing: Used for cosmetic appeal in consumer electronics.
These finishing options allow manufacturers to align the part’s appearance and function with the end-user expectations.
Design Tips for CNC Aluminum Parts
To ensure high-quality outcomes in cnc aluminum parts, keep the following in mind during design:
- Avoid Thin Walls: Thin sections can vibrate or deform during machining.
- Use Uniform Wall Thickness: Prevents uneven stress and improves strength.
- Add Fillets and Radii: Sharp internal corners are hard to machine; rounded corners ease tool movement.
- Minimize Deep Cavities: Deep slots may require specialized tools and increase cost.
Consulting with CNC engineers during the design phase helps optimize manufacturability and reduce costs.
Trends in CNC Aluminum Parts Production
With the ongoing evolution of smart manufacturing, several trends are shaping the future of cnc aluminum parts:
🔄 Automation
Automated tool changers and robotic arms are improving productivity in CNC shops.
🌍 Sustainable Manufacturing
Recycling aluminum chips and using energy-efficient CNC systems is becoming standard.
🧠 Smart Machining
AI-powered software can predict tool wear, adjust feeds in real time, and reduce waste.
📦 Online Quoting and On-Demand Production
Digital manufacturing platforms allow customers to upload CAD files and receive instant quotes, streamlining the procurement process.
Final Thoughts
In today’s innovation-driven economy, cnc aluminum parts offer a rare combination of material excellence and manufacturing precision. From small startups developing prototypes to multinational corporations launching advanced tech products, the demand for high-performance, reliable components has never been higher.
CNC machining brings out the full potential of aluminum, delivering parts that are strong, lightweight, corrosion-resistant, and cost-effective. As technology continues to advance, so will the applications and performance of cnc aluminum parts, keeping them at the forefront of modern manufacturing solutions.